Акустический короб под блины — Opel Omega, 2.0 л., 1997 года на DRIVE2
Надоело просто так сидеть дома, решил заняться какой нить фигнёй)
Как то давно, может месяц назад один мой знакомый купил автомобиль: некую семочку за 45 000 российской валюты… Ну вот а сам больно то не ездит, боится, т.к. давно за рулём не сидел, приехал я как то навестить его, переставили мы его Тачку, немного поржали, ну и начали расходиться по домам) Но вдруг он стал беспокоиться за свои колонки (блинчики), мол сигналки то нет, вдруг стащат… Ну значит давай их снимать… А головы (магнитолы) у него всё равно нет ну я и предложил, мол дай их мне, а то дырки в полке есть (от старого владельца), а колонок нету… После недолгих уламываний я позаимствовал у него эти самые колоночки, под предлогом что по первому звонку я ему их верну…
Собственно вот они:

Calcell cp-6930
Так вот, и начал я под них делать этот самый короб… Ну имея 5 по черчению мне это ещё и в удовольствие) (Нравятся все эти точные расчёты, и что-то конструировать)…
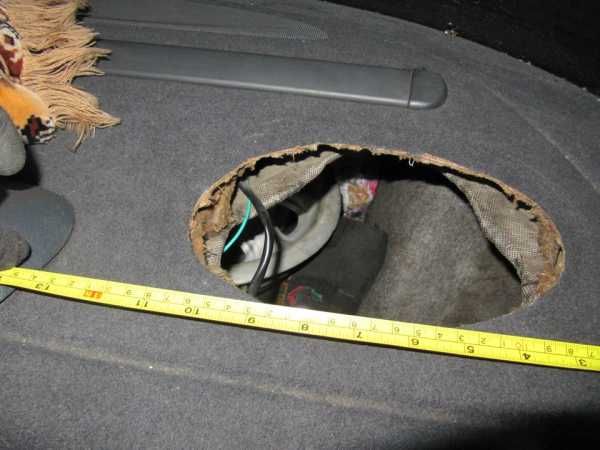
Полочка с дыркой)

Полочка с дыркой)
я приступил к работе…
На чертеже создал фронтальный, горизонтальный и вид сверху, что бы всё точненько получилось… Создал в размере трёхмерный эскиз (прошу прощения но его фотографии нет, забыл сфотографировать, а когда опомнился его уже не было, разорвал, и помял весь(), достал пилу, ДСП и начал мусорить)

опилочки
Дабы сильно не пылить, я использовал пылесос по назначению)
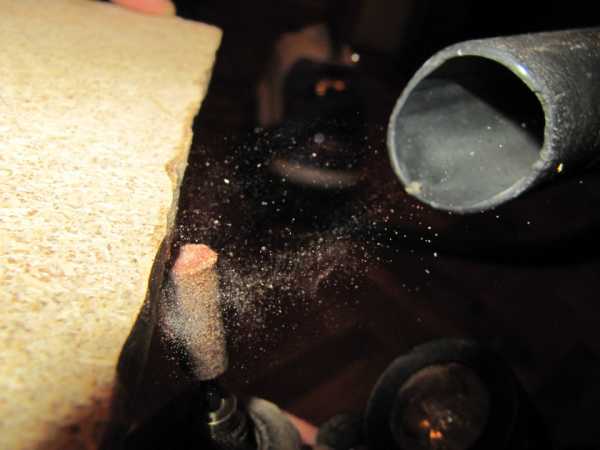
Отсос
Резали-резали, Пилили-Пилили

SAW
Что-то не получалось, приходилось лишние куски выбрасывать, и вырезать новые… Но вот спустя пару часов точной и кропотливой резки у меня в руках появились стенки и дно… Собрав её, присмотревшись, я был удовлетворён результатом,
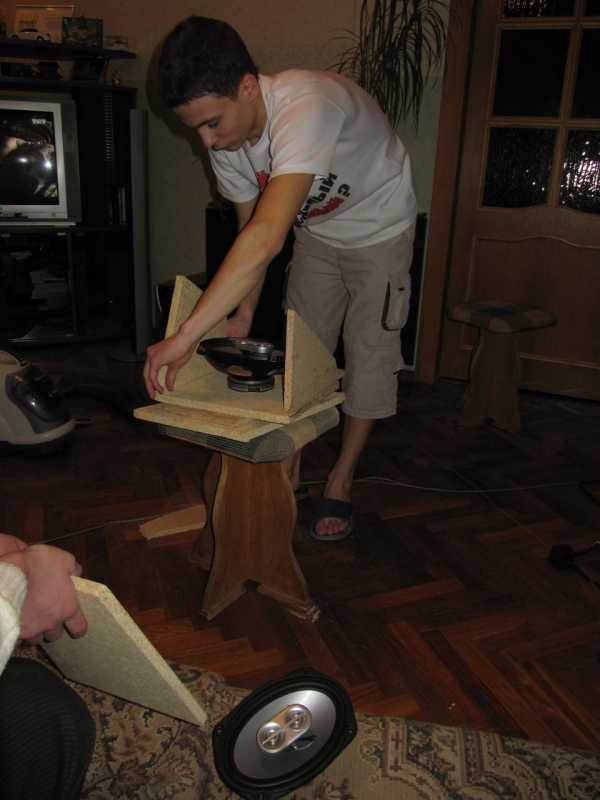
Удовлетворение
и после небольшого отдыха (по телеку начался мультик Джимми-Нейтрон =D)

отдыхаем
я снова приступил к работе… Измерив парочку данных

измеряем-проверяем
я начал пилить «лицо» и пото
www.drive2.ru
Короба для саба и колонок своими руками — Лада 2107, 1.6 л., 2004 года на DRIVE2
Как -то решил музыку поставить в Семку. Думал куплю магнитолу, усь и саб. Думал збс будет, потом друг посоветовал в студию заехать узнать, что и где купить. Приехали, и поняли, что мы лохи полнейшие)) Нам сказали, то что вы собрались покупать полное Гавнище и играть не будет вообще ни как)) Затем, они подогнали варианты подходящие для меня. Выбрал я самый дорогой) + сказал, что короба сам буду собирать) Колонки передние на двери не собирался вешать так как двери провисают да и ногами их все пинают, следовательно было решено колонки под сиденья передние. С коробом для саба проблем не возникло-65 литров спокойно в багажник влезут, а вот с колонками пришлось попотеть, думал, сначала прост сделать квадратный короб, но звук был бы направлен не туда куда нужно…
Короба делал из ДСП 16мм. Саб делал в два слоя, колонки в один слой. Саб — 32 мм, колонки- 16мм. Не было в городе на тот момент фанеры 25мм =(. Не советую делать из ДСП никому! Очень сложно, она крошится, если саморез криво пойдёт. Да и получается, что я саб два раза собирал. Между собой склеивал ДСП клеем ПВА строительным и сжимал саморезами каждые 10-7см.

фото 3
Сдвоил все стенки саба, потом началось самое сложное, соединить их. Это просто АД! Чтоб ДСП не трескалась от самореза в ней нужно просверлить отверстие под каждый саморез, и лишь потом вкручивать саморез. Сверлил сверлом 2мм, переломал свёрл 10 точно, стенки соединял змейкой, так как ДСП склеена, то в центр саморез вкручивать нельзя.
фото 2
У саба есть стенки, соеденяющиеся под углом, их сложнее всего соеденять, так как саморез так же должен соеденять сненки под углом. Но с этим я более менее справился… Затем, герметил всё, ушло 10 тюбиков по 180гр., 400 саморезов на саб, 100 на колонки и кучу времени. В сабе и колонках фазинверторы, в сабе 100мм диаметр, в колонках 50мм.Всё собрал, закрепил колонки и саб в коробах, щас проводку делаю, креплю усилители и кроссоверы. Короба получились отменные! Хоть и из фанеры 25мм легче делать, зато звук при сдвоенной ДСП лучше! Короб под саб весит 45 кг. =)
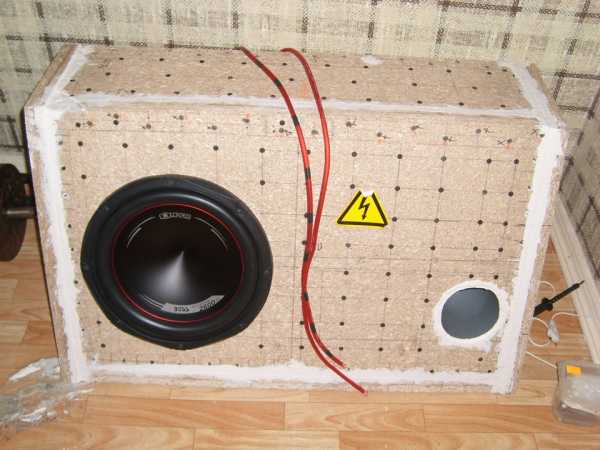



www.drive2.ru
Короба для колонок под сиденья — Лада 2102, 1.2 л., 1977 года на DRIVE2
давно хотелось не громкой качественной музыки в классику, да и так чтобы и карты не резать и вид не портить
тут подвернулось на халяву пару колоночек нулёвых DLS Matador 1369 6×9″
ну так се, для классики пойдет)) ахах
до этого имелся усилок Fusion fe-505… ну так тоже сойдет)))
прикупил магнитолку Sony Xploid с пультом
решил собрать короба под сидния, размеры везде есть, легко найти
UPDATE
жесть, оказывается не так уж и легко их найти… как говорят…
все размеры считаются строго по СВОЕЙ акустике! под свои ваты, диаметры дифузоров и тп…
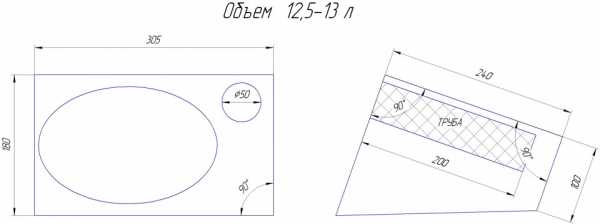
.
с другими колонками будет играть по другому!
с помощью програмки BassPort расчитал все параметры… литраж под колонки, длину/диаметр фазоинвертора и все остальное…
прикупил:
1. ДСП 16 мм
2. Герметик
3. Саморезы
4. пластиковую трубу
5. водоотталкивающая пропитка для дерева

1
запилил по размерам, пропитал Барьером

2
промазал швы герметиком

3
отрезал кусок трубы по расчитанной длине, вставил, промазал герметиком
посадил колонки на герметик, прикрутил саморезами

4
получилось что то такое

5
мля, вот не давали руки покоя, все время сомневался в точности расчетов из программ, а зря)
перепробывал кучу вариантов длинны и позиции фазоинвертора, но качественный звук получился как раз только по расчетам)
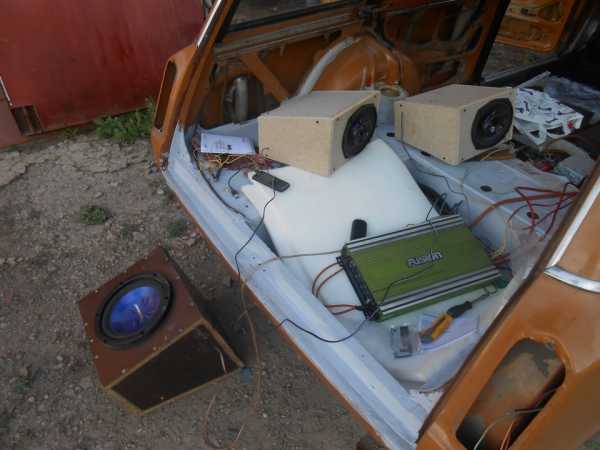
5
магнитолку положил пока в бардачок, с местом еще не определился, но на торпеде ничего не будет!
прикинул все, послушал, ах*ел )) и поставил на места)
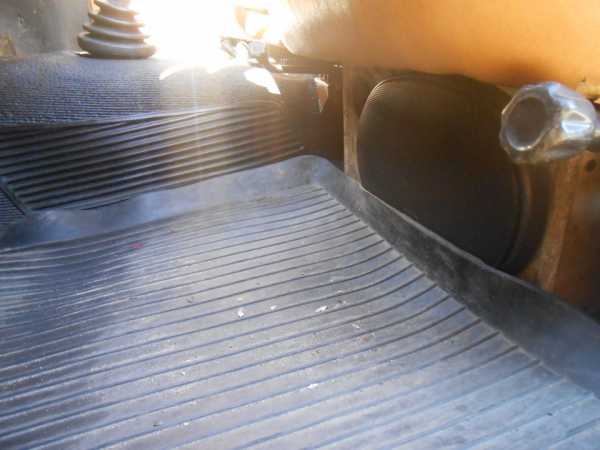
_

www.drive2.ru
ЧВ для дома. Рассчитываем и собираем. — Сообщество «Автозвук» на DRIVE2
Всем привет! В это записи расскажу о постройке ЧВ (четвертьволновой резонатор) Так же расскажу как его рассчитать. Первым делом нужно найти подходящий динамик, для ЧВ лучше подойдут динамики с большим подвесом, т.к. в таком оформлении ход динамика больше чем в остальных. Если вы собираете ЧВ для дома, гаража и т.п., то вполне хватит 13, 16-ти см. динамика. Мне под руку попался 13-ти см. мид Infiniti

Infiniti справа, слева 16-ти см. динамик из обычного домашнего сабика
Далее рассчитываем короб: Находим эффективную площадь диффузора, (для дальнейшего расчета площади сечения порта) для этого измеряем расстояние от середины подвеса до противоположной середины. Это у нас получился диаметр.
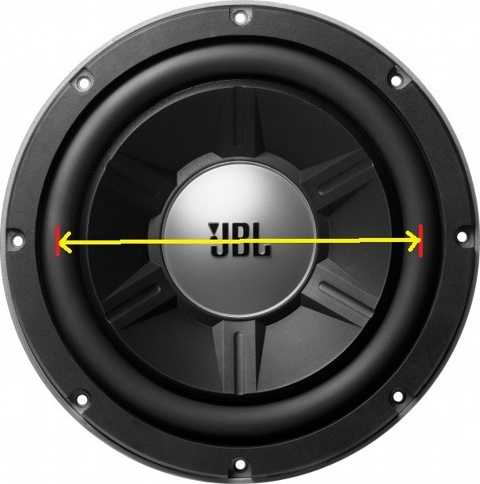
Измеряем это расстояние
Думаю как находить площадь круга все знают, 3.14*R^2 В моем случае получилось 103.8 см. кв.
Затем получившееся число умножаем на 1.5, этим мы находим площадь сечения порта. 103.8*1.5=156 см. кв. Теперь исходя из своих предпочтений выбираем высоту и ширину порта, нужно только учесть чтобы в одну из сторон убралось установочное отверстие динамика, а в другую установочная глубина динамика. Не стоит делать порт слишком узким, сечение должно быть ближе к квадрату и прямоугольнику. Я решил сделать так, высота 15.6 см., ширина 10 см., умножаем и получается 156 см. кв.
Далее определимся с настройкой, как правило нужно настраивать близко к резонансной частоте (Fs) динамика, но как показывает практика людей, не стоит настраивать ЧВ с маленькими динамиками низко, для 13-ти см. динамика подойдет настройка 50 Гц. Значит с настройкой определились, теперь находим длину порта, её находим по формуле (343/настройка)4, в нашем случае будет выглядеть так (343/50)/4=1.72 м.
Теперь сворачиваем порт, только учтите чем меньше поворотов, тем эффективнее ЧВ. Длина считается по середине порта

вот таким образом
Скругления углов делайте обязательно, только учтите, что при скруглении — длина порта уменьшается!
Для удобства расчета короба скачайте программу Google SketchUp 8, в ней очень удобно моделировать. При расчете учтите ещё и толщину используемого материала.
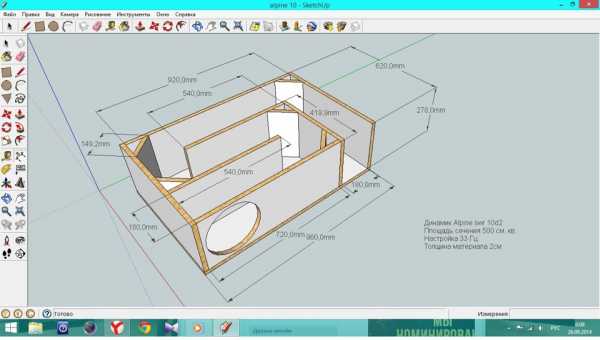
Готовый чертеж на примере динамика Alpine SWR 10D2
Теперь перейдем непосредственно к сборке
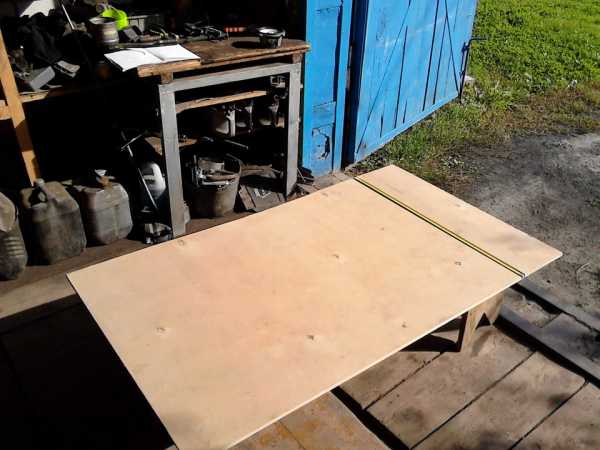
Используемый материал фанера-14 мм.
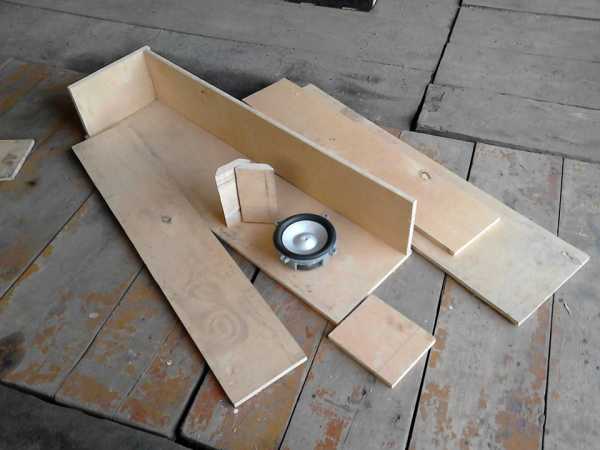
напилил

собрал
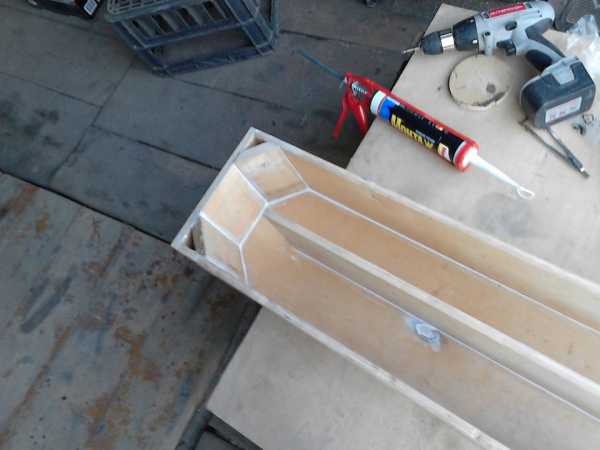
Все стыки промазываем герметиком

Устанавливаем динамик

тянем проводку

Красим порт и обклеиваем карпетом

Готово!
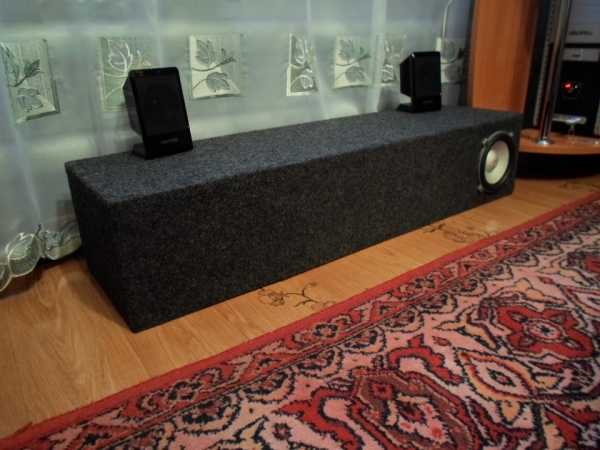
уже дома
Теперь что мы имеем. Играет очень приятно, даже не низких негров, в машине пытается потряхивать зеркала. Бас очень насыщенный быстрый, сам не ожидал такого эффекта от этого малыша, до этого играл в ЗЯ, звук совсем другой. Превосходно играет клуб, дабстеп. Когда играл в гараже, все помещение было наполнено басом. Знакомые очень удивлялись, когда слышали как он поёт. Вот небольшое видео vk.com/id141885528?z=vide…0006701%2Fvideos141885528 В общем если вы хотите достойную музыку, с умеренным басом, в дом, машину. пилите ЧВ) Спасибо за внимание! Комментарии приветствуются)
Добавил чертёж
www.drive2.ru
Короб для колонок. — Opel Calibra, 2.0 л., 1991 года на DRIVE2
Доброго времени суток .Этот пост хочу посветить моему первому опыту в сфере стекловолокна, т.к полку я сделал не акустической и соответственно колонок в ней нет, встал логичный вопрос куда засунуть мои две маленькие колоночки=). Выбор пал на багажное отделение, но просто квадратную коробуху не очень хотелось(насмотревшись в инете красивых картинок, очень захотелось попробовать что то из стекловолокна).Так вот, просидев пару ночей за компом и просмотрев кучу роликов как все это можно «слепить» я побрел в гараж воплощать свой план в жизнь).
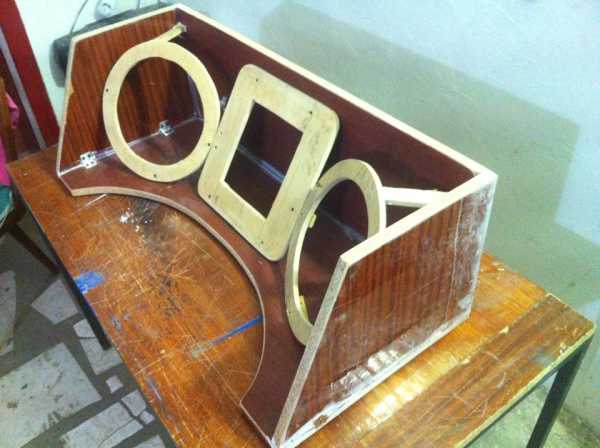
Слепил каркас для колонок и усилителя(хотелось именно колонки поставить, саб есть, но я не захотел.)
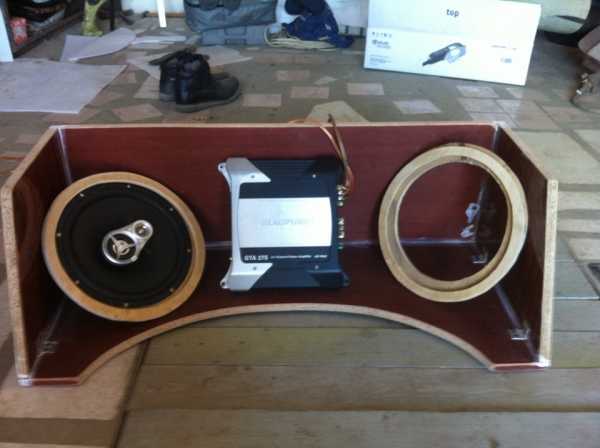
Это вид колонок и усилка в их первозданном виде(в процессе их пришлось чуточку переделать).

Затянули все это

Весь процесс описывать не буду, вот результат уже зашпаклеван.
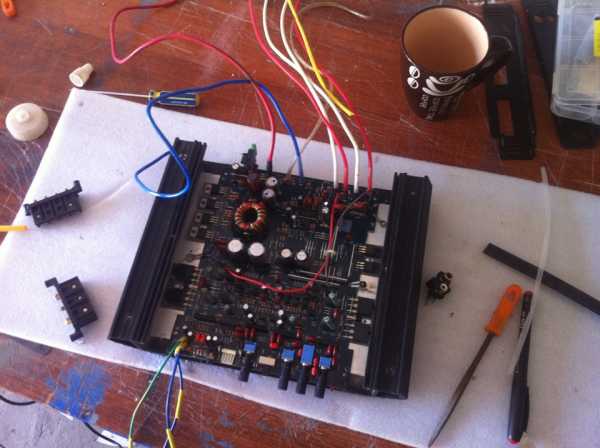
А вот и наши переделки, пришлось вмешаться в устройство усилка т.к все контактные клеммы были по бокам, а мне это не очень нравилось(перенесены на заднюю крышку).
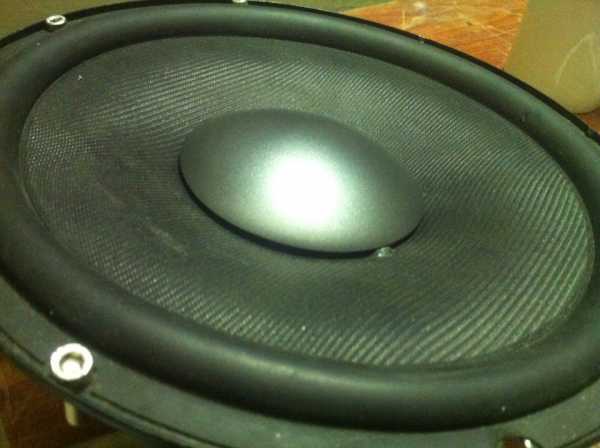
Колонки тоже модернизировались, были удалены пищалки, а взамен из пвх изготовили центральные пятаки и затянули их пленкой.

Внедрили

А вот и результат, а еще заменил старый пол на новый ковролин.
Сильно не пинайте, это мой первый опыт). Конечно я понимаю, что если б его покрасить намного лучше смотрелось, но я наверное малярку не осилил(пока еще=)).
Всем спасибо за внимание.
www.drive2.ru
Короба под колонки. — Лада 2101, 1.3 л., 1980 года на DRIVE2
Привет, друзья=)
Однажды мне позвонил знакомый, который подогнал для моей машины 4 колеса с колпаками, и сказал, что нашел немного ненужных ему запчастей и просил их забрать. При встречи он передал мне детали, но опять отказался взять за них деньги. Я ему сказал спасибо и пожал руку. Мужичек обратил внимание, что в моей копейке на задней полке стоят короба с колонками и спросил есть ли у меня еще такие, но большего размера. По моей просьбе он принес одну колонку. Оказалось, что она JBL на 300 Вт. В ходе небольшого разговора выяснилось, что ему очень не хочется пилить заднюю полку, так как это займет очень много времени. Я же в свою очередь похвалил его, за то что еще не начал кромсать машину и предложил изготовить короба из фанеры. По началу мужичек не хотел меня утруждать данной работой, но я все же настоял на своем и тот согласился.
Дома нашел несколько обрезков 10 мм фанеры и небольшой кусок 6 мм фанеры. Тонкая фанера стала площадкой под колонку, а из десятки сделал стенки. Конструкция собрана так, чтобы динамик колонки был поднят на 0,5 — 1 см и не касался полки. Соединял конструкцию черными 32 саморезами по дереву. Предварительно в местах вкручивания самореза делал небольшие отверстия 3-х мм сверлом, чтобы шуруп не расщепил фанеру. 8 мм сверлом углублял посадочное место по шляпку самореза. Ткань была в наличии. Материал сшивался на швейной машинке по всем граням короба. Фиксировался сшитый материал 6 мм скобами.
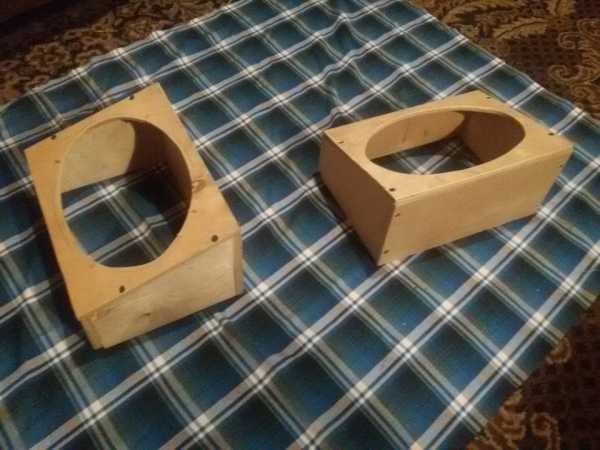



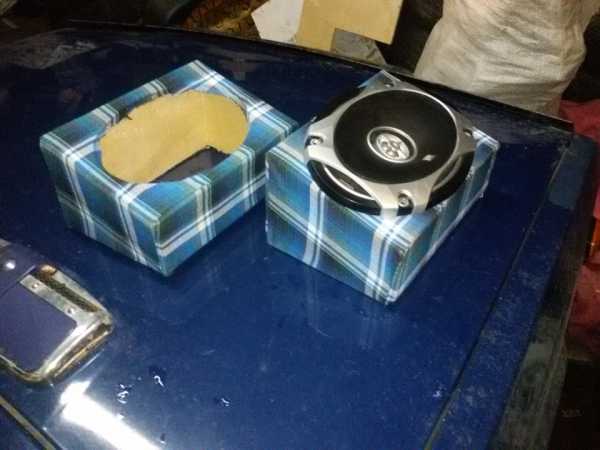
Так как колонка сама по себе тяжелая, поэтому изготовил дополнительные крепления из алюминиевой пластины. Примерку и подгонку креплений проводил в своей машине. И так, что получилось: короба собраны, легко устанавливаются и снимаются, динамик идеально лежит на коробе и полки не касается, между сиденьем и задним стеклом есть зазоры, сиденье легко снимается и устанавливается обратно. Самое главное — данная установка короба не требует резки и порчи задней полки. Очередная задумка осуществлена=) Спасибо за внимание=)
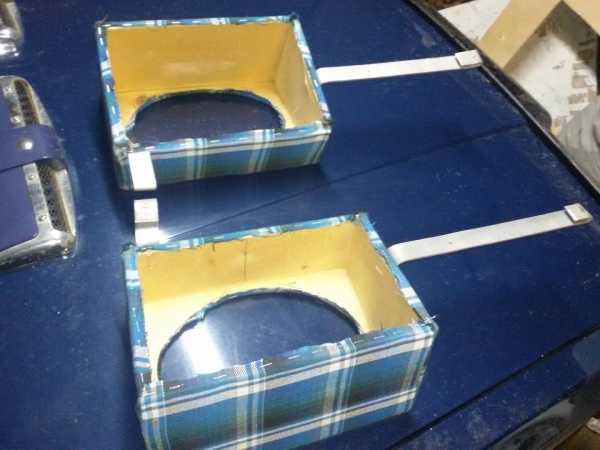

www.drive2.ru
Обзор материалов / Аудиомания corporate blog / Habr
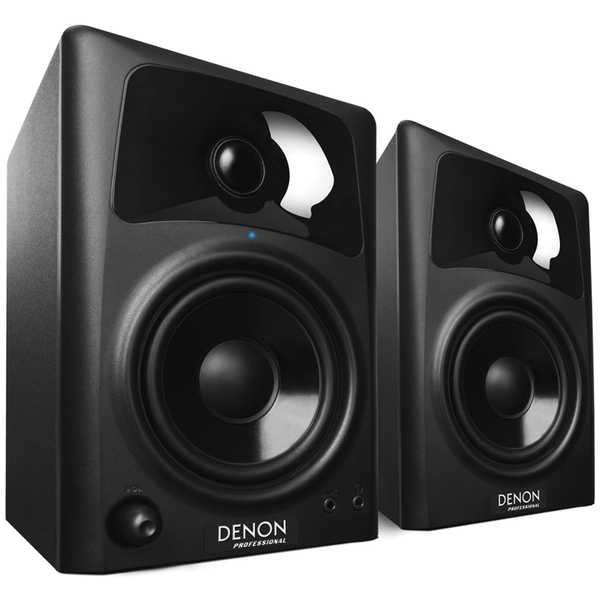
Профессиональная активная акустика Denon DN-304S
Раньше колонки представляли собой обыкновенные рупорные громкоговорители и не имели корпуса как такового. Все изменилось, когда в 20-х годах XX века появились динамики с бумажными диффузорами.
Производители начали изготавливать крупные корпуса, которые вмещали в себя всю электронику. Однако вплоть до 50-х годов многие производители аудиоаппаратуры не закрывали корпуса колонок полностью – задняя часть оставалось открытой. Это было связано с необходимостью охлаждения электронных компонентов того времени (ламповое оборудование).
Задача корпуса колонок – контроль акустической среды и удержание динамиков и других компонентов системы. Уже тогда было замечено, что корпус способен оказывать серьезное влияние на звучание громкоговорителя. Поскольку передняя и задняя части динамика излучают звук с разными фазами, то возникала усиливающая или ослабляющая интерференция, что приводило к ухудшению звука и появлению эффекта гребенчатой фильтрации.
В связи с этим начались поиски способов улучшения качества звучания. Для этого многие стали исследовать естественные акустические свойства различных материалов, пригодных для изготовления корпусов.
Волны, отраженные от внутренней поверхности стенок корпуса колонок, накладываются на основной сигнал и создают искажения, интенсивность которых зависит от плотности используемых материалов. В связи с этим часто оказывается, что корпус стоит гораздо дороже компонентов, заключенных в нем.
При производстве корпусов на крупных фабриках, все решения касательно выбора формы и толщины материалов принимаются на основании расчетов и тестов, однако Юрий Фомин, звукоинженер и инженер-конструктор акустических систем, чьи разработки лежат в основе мультимедийных систем под брендами Defender, Jetbalance и Arslab, не исключает, что даже в отсутствие специальных музыкальных знаний и большого опыта работы в аудиоиндустрии можно сделать что-то, близкое по характеристикам к «серьезному» Hi-Fi.
«Надо брать готовые разработки, которыми инженеры делятся в сети, и повторять их. Это 90% успеха», – отмечает Юрий Фомин.
При создании корпуса акустической системы следует помнить, что, в идеале, звук должен поступать только из динамиков и специальных технологических отверстий в корпусе (фазоинвертор, трансмиссионная линия) – нужно позаботиться, чтобы он не проникал через стенки колонок. Для этого рекомендуется выполнять их из плотных материалов с высоким уровнем внутреннего звукопоглощения. Вот несколько примеров того, из чего можно собрать корпус для динамиков.
Древесно-стружечная плита (ДСП)
Это доски, сделанные из спрессованной древесной стружки и клея. Материал обладает гладкой поверхностью и неплотной рыхлой сердцевиной. ДСП хорошо гасит вибрации, однако пропускает через себя звук. Плиты легко скрепляются клеем для дерева или монтажным клеем, однако их края имеют тенденцию крошиться, что немного усложняет работу с материалом. Также он боится влаги – при нарушении производственных процессов легко её впитывает и разбухает.
В магазинах продают доски разной толщины: 10, 12, 16, 19, 22 мм и так далее. Для небольших корпусов (объемом меньше 10 литров) подойдет ДСП толщиной 16 мм, а для корпусов большего размера следует выбрать доски толщиной 19 мм. ДСП можно облицовывать: обклеивать пленкой или тканью, шпаклевать и красить.
Древесно-стружечная плита используется при создании акустической системы Denon DN-304S (на фото выше). Производитель выбрал ДСП потому, что этот материал является акустически инертным: колонки не резонируют и не окрашивают звук даже при высокой громкости.
Облицованная ДСП
Это ДСП, облицованная декоративными пластиками или шпоном с одной или с двух сторон. Плиты с деревянной облицовкой скрепляются обычным клеем для дерева, однако для ДСП, облицованной пластиком, придется покупать специальный клей. Для обработки срезов доски можно воспользоваться кромочной лентой.
Столярная плита
Популярный строительный материал из реек, брусков или других наполнителей, которые оклеены с двух сторон шпоном или фанерой. Плюсы столярной плиты: относительно малый вес и простота обработки краев.
Ориентированно-стружечная плита (ОСП)
ОСП – это доски, спрессованные из нескольких слоев тонкой фанеры и клея, узор на поверхности которых напоминает мозаику желтого и коричневого цветов. Сама поверхность материала неровная, но ее можно отшлифовать и покрыть лаком, поскольку текстура дерева придает этому материалу необычный вид. Такая плита обладает высоким коэффициентом звукопоглощения и устойчива к вибрациям.
Древесноволокнистая плита средней плотности (МДФ)
Сделанный из древесной стружки и клея, этот материал более гладкий, чем ОСП. Благодаря своей структуре МДФ хорошо подходит для изготовления дизайнерских корпусов, поскольку легко поддается распилу, – это упрощает стыковку деталей, скрепляемых между собой при помощи монтажного клея.
МДФ можно облицовывать, шпаклевать и красить. Толщина плит варьируется от 10 до 22 мм: для корпусов колонок объемом до 3 литров будет достаточно доски толщиной 10 мм, до 10 литров – 16 мм. Для больших корпусов лучше выбрать 19 мм.
Если при выборе материала для изготовления корпусов акустических систем отбросить в сторону звуковые аспекты, то останутся три определяющих параметра: низкая стоимость, простота обработки, простота склеивания. МДФ как раз обладает всеми тремя. Именно невысокая стоимость и «податливость» МДФ делают его одним из самых популярных материалов для изготовления колонок.
Пример использования МДФ – полочная акустика Arslab Classic 1 SE, стенки корпуса которой изготовлены из толстых древесноволокнистых плит, препятствующих возникновению вибраций и окрашиванию звука.
Фанера
Этот материал сделан из спрессованного и склеенного тонкого шпона (около 1 мм). Для повышения прочности фанеры слои шпона накладываются так, чтобы волокна древесины были направлены перпендикулярно волокнам предыдущего листа. Фанера – лучший материал для подавления вибраций и удержания звука внутри корпуса. Склеить фанерные доски между собой можно обычным клеем по дереву.
Шлифовать фанеру сложнее, чем МДФ, поэтому выпиливать детали нужно как можно точнее. Среди достоинств фанеры стоит выделить её легкость. По этой причине из неё часто делают кейсы для музыкальных инструментов, ведь достаточно обидно отменять концерт из-за того, что музыкант надорвал спину.
Именно этот материал применяется компанией Penaudio для производства напольной акустики – она использует латвийскую фанеру, которая изготавливается из березы. Многим нравится то, как выглядит обработанная березовая фанера, особенно после покрытия лаком, – это придает корпусу уникальности. Этим и пользуется компания: поперечные слои фанеры стали своеобразной «визитной карточкой» Penaudio.
Напольная акустика Penaudio Rebel Three
Камень
Чаще всего используются мрамор, гранит и сланец. Сланец – самый подходящий материал для изготовления корпусов: с ним достаточно просто работать из-за его структуры, и он эффективно поглощает вибрации. Главный недостаток – необходимы специальные инструменты и навыки обработки камня. Чтобы как-то упростить работу, возможно, имеет смысл изготовить из камня только переднюю панель.
Стоит отметить, что для установки колонок из камня на полку, вам может понадобиться мини-кран, да и сами полки должны быть достаточно прочными: вес каменной аудиоколонки достигает 54 кг (для сравнения, колонка из ОСП весит около 6 килограмм). Такие корпусы серьезно улучшают качество звука, но их стоимость может оказаться «неподъемной».
Колонки из цельного куска камня делают ребята из компании Audiomasons. Корпусы вырезаются из известняка и весят порядка 18 килограмм. По заявлениям разработчиков, звучание их продукта придется по вкусу даже самым искушенным меломанам.
Оргстекло/стекло
Можно сделать корпус для динамиков из прозрачного материала – это действительно круто, когда видно «внутренности» колонки. Только здесь важно помнить, что без должной изоляции звук будет ужасным. С другой стороны, если вы добавите слой звукопоглощающего материала, прозрачный корпус перестанет быть прозрачным.
Неплохим примером акустической hi-end-аппаратуры из стекла может служить Crystal Cable Arabesque. Корпуса техники Crystal Cable изготавливаются в Германии из полос стекла толщиной 19 мм со шлифованными гранями. Детали скрепляются между собой невидимым клеем в вакуумной установке, дабы избежать появления пузырьков воздуха.
На выставке CES-2010, проходившей в Лас-Вегасе, обновлённые Arabesque завоевали все три награды в области Инноваций. «До сих пор ни одному производителю техники не удавалось добиться настоящего hi-end-звучания от акустики, изготовленной из такого сложного материала. – писали критики. – Компания Crystal Cable доказала, что это возможно».
Клееная древесина/дерево
Из дерева получаются хорошие корпуса, однако здесь нужно учитывать важный момент: дерево имеет свойство «дышать», то есть оно расширяется, если воздух влажный, и сжимается, если воздух сухой.
Так как деревянный брусок проклеивается со всех сторон, в нем создается напряжение, что может привести к растрескиванию древесины. В этом случае корпус потеряет свои акустические свойства.
Металл
Чаще всего для этих целей используется алюминий, точнее – его сплавы. Они легкие и жесткие. По мнению ряда специалистов, алюминий позволяет уменьшить резонанс и улучшить передачу высоких частот звукового спектра. Все эти качества способствуют росту интереса к алюминию со стороны фирм-производителей аудиоаппаратуры, и его используют для изготовления всепогодных акустических систем.
Существует мнение, что изготовление цельнометаллического корпуса – не самая хорошая идея. Однако стоит попробовать сделать из алюминия верхние и нижние панели, а также перегородки жесткости.
Наши материалы по теме:
habr.com